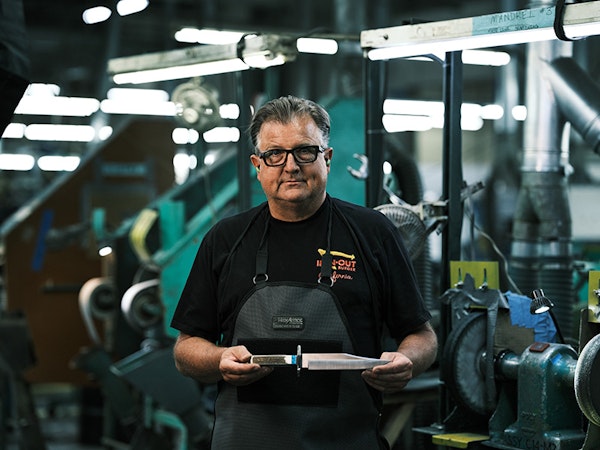
The pocket knives department needed more help. Demand for some of the staple models from Buck Knives was through the roof in 1988. Luckily, a new employee arrived to build those knives by hand. He had no experience with knives at the time, but he was a fast learner and had the mechanical ability. Jim Whyte had always liked to build things. The new opportunity at Buck allowed him to combine getting his hands dirty and learning a new trade. As an amateur mechanic and handyman, a pocket knife was never far away from Whyte. It was a perfect fit.
It did not take Whyte long to move from pocket knives to Department 13. This is the department where classic fixed blades are constructed. The 119 Special, the 120 General, and the famed hunting bowie knife recognized throughout the knife world, the 124 Frontiersman, were now under Whyte’s fingertips. His technical skills were honed with the smaller, more fragile pocket knives, but this is where knifemakers gain respect. “Now that’s a knife,” in an Australian accent comes to mind. But these were not the most recognizable knives from the Buck Knife family, and Whyte had his eye on another department after a few years.
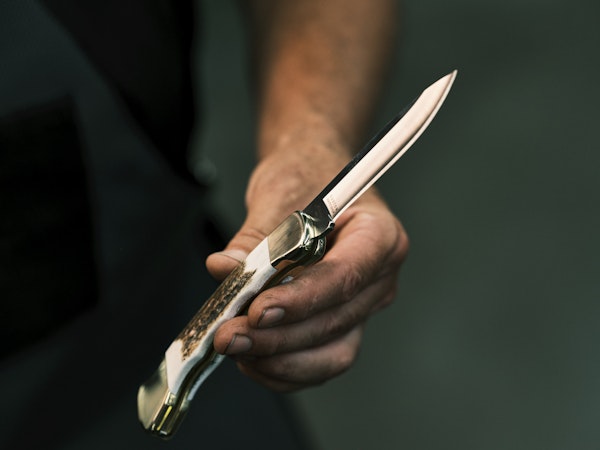
Whyte had to get his hands on the one knife that put Buck on the map. The knife that remains one of the best sellers, 60 years after its inception, and has inspired countless configurations of other models. He finally got to work in Department 01. Building a 110 Folding Hunter for Buck Knives is a rite of passage. It is sturdy enough to handle any workload, but with components that require attention to detail and precise knowledge of the knifemaking process. Whyte developed his true craftsmanship over the next 20 years in Department 01. During that stint he moved with the company up to Post Falls, Idaho, because he had found a passion within his career.
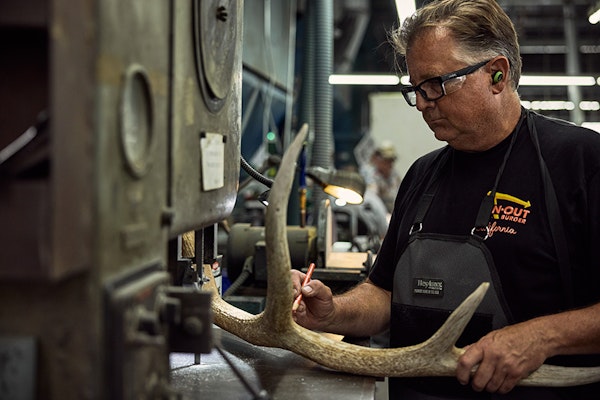
After Whyte relocated with Buck Knives, he also repositioned to the Custom Knife Shop. All of his experience with core products, wood inlays, various bolster metals, and a myriad of steel finishes would be put to use. The options at the Buck Knives Custom Knife Shop stand out. Here, Whyte learned how to shape full elk sheds, buffalo horns, and ironwood into handle material. He crafted aluminum and brass guards, chipflint and mirror polished blades, and developed the next level of craftsmanship only a 30-plus-year knifemaking veteran could achieve. Each knife is hand cleaned and inspected, then accompanied by a signed certificate of authenticity when shipped. “That means quite a bit to the operator that made it and the customer receiving it on the other end. They’re kind of connected that way,” Whyte claims. After 35 years of knifemaking, Jim Whyte occasionally takes his work for granted. He forgets that experience and dedication are the only reasons these knives garner such respect. “Customers come by on tours and I can see it in their eyes, they’re just in awe. I am really proud to create these knives,” Whyte said.